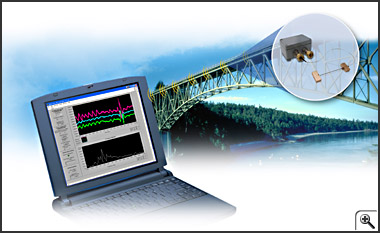
Researchers are studying many future applications for wireless microsensors, devising technology and procedures for bringing paralyzed limbs back to life, harnessing electricity from bending materials and magnetism, and remote monitoring of bridges and cargo for safety and homeland security.
The Department of Health and Human Services is supporting researchers at Case Western Reserve University as they experiment with MicroStrain EmbedSense orientation-monitoring sensors. The wireless devices may eventually help coordinate systems that re-animate paralyzed limbs. EmbedSense can be powered by magnetism through a property called inductance—the wearer moves a magnetic rod near the magnetic receiving end on the device implanted in their body. The movement induces a flow of electric current, providing power to the surgically implanted device.
Meanwhile, some of MicroStrain’s newest experiments are exploring power methods that use bending to create electric current. Called piezoelectricity, some objects create electric current when they bend, and conversely bend when they are fed an electric current. The mineral quartz is piezoelectric, and the latter property is what causes the quartz crystal in a watch to vibrate consistently, producing the counts that keep the watch on time.
MicroStrain researchers are adapting the concept to extract enough movement from the shaking of bridge beams or the straining of the walls of ships to power networks of monitoring sensors. Devoid of the need for maintenance, the sensors could continuously provide information about damage to and strain on both our national infrastructure and our military vessels.
Students at the University of Vermont are collaborating with company engineers to monitor stresses on a local bridge using wireless sensors and transmitters that could one day benefit from piezoelectrically-powered devices. A network of sensors on the bridge tracks and records data from strains initiated by the overhead traffic. A transmitter mounted near the sensors collects the data and transmits it via cellular phone signal to the Internet, where engineers monitor the results in their laboratories.
In the not-so-distant future, such a procedure could become commonplace, with wireless sensors monitoring stresses and warning operators well in advance of a potential structural failure. Municipal workers could repair the structure well before there is a danger and prevent a catastrophic bridge or building collapse.
Finally, integrated sensor networks could eventually help monitor cargo en route to the U.S. to prevent tampering and security breaches. Currently, agents at our borders can only monitor 2% of cargo, with standard containers measuring a daunting 40 feet in length and weighing 20 tons—and some ships carrying as many as 5000 of them.
Some devices coming online, such as the truck-sized, National Science Foundation Small Business Innovation Research (SBIR) supported ARACOR Eagle can scan the cargo crates, many in less than a minute, detecting contraband, stowaways, and potentially threatening chemical or explosive agents. However, if the cargo can be monitored by agents from the moment of shipping, the cargo is more likely to be secure on arrival (and potentially threatening crates can be inspected safely offshore).
MicroStrain currently envisions a set of devices that would consist of a master sensing and communication node, door intrusion sensors, and wireless remote sensing nodes. The system could be monitored via the web, with the sensors revealing opening of cargo doors en route and inertial navigation and global positioning system components revealing whether or not the boat stopped at an unauthorized location.
** Photo Credits:
-- MicroStrain, Inc.
-- Advanced Research and Applications Corporation (ARACOR); National Science Foundation
|